Vertical grinder mills – BMH range
In 1975, Danieli Henschel developed vertical grinder mills so that its customers could obtain an output product of unparalleled quality compared to all other equipment – shears, presses, and Hammermill type shredders – available on the market.
More and more metal recycling companies are looking for a compact shredding installation to satisfy the demands of the steel industry. These companies have thus expressed the need to obtain a certain type of shredded metal waste: cooling scrap, which is used as a cooling mass for the liquid steel baths employed in the process at steel works.
The range was also developed to process different product categories to suit the needs of our customers.
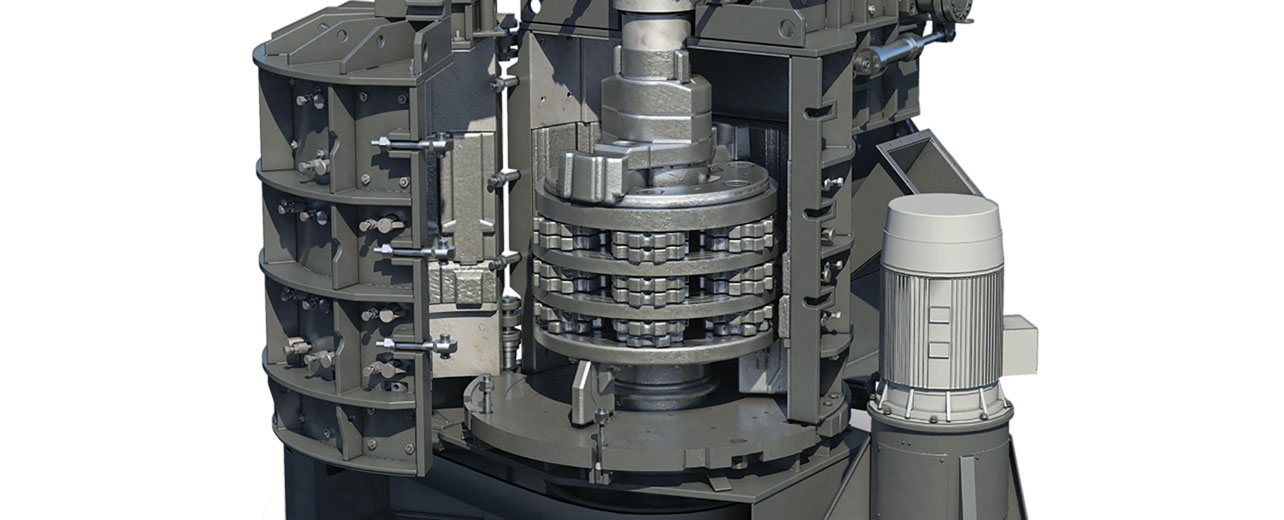
Final product complying with the highest standards of the steel industry regarding quality.
Densification of the final product up to 3.5 t/m3, allowing use for specific applications, e.g. as cooling scrap in metallurgical processes.
Refining of especially polluted incineration scrap, after screening.
Optimisation of wear thanks to the two-way rotor.
Robust design guaranteeing low maintenance costs.
With its tremendous versatility, it addresses many problems.
Densification of the final product up to 3.5 t/m3, allowing use for specific applications, e.g. as cooling scrap in metallurgical processes.
Refining of especially polluted incineration scrap, after screening.
Optimisation of wear thanks to the two-way rotor.
Robust design guaranteeing low maintenance costs.
With its tremendous versatility, it addresses many problems.
Hardening the material by crushing it against a wall using a rotor equipped with manganese steel star cams.
Two to three reduction stages, with gradual densification of the product from one level to the next.
Evacuation of unshreddable material via hydraulic exit door.
Easier release of the various shredded components.
Separation of lightweight sterile waste by ventilation.
Regular and uniform output flow without risk of excess accumulation.
Two to three reduction stages, with gradual densification of the product from one level to the next.
Evacuation of unshreddable material via hydraulic exit door.
Easier release of the various shredded components.
Separation of lightweight sterile waste by ventilation.
Regular and uniform output flow without risk of excess accumulation.

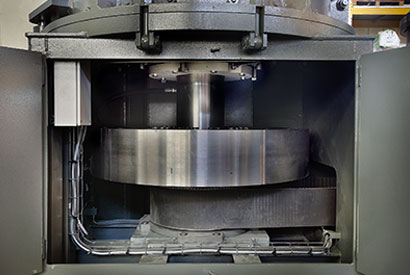
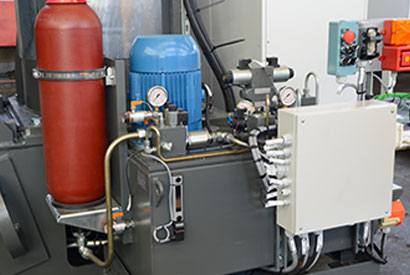
Ergonomics
- Installation according to customer requirements
- Compact hydraulic units
- Human/machine interface by touch screen display
- Small footprint
Working life
- Robust, reinforced design
- Casing protected by abrasion-resistant plates and manganese steel shielding parts
- Reinforced protection:
> of the motor, via hydraulic coupler,
> of the transmission, via notched flexible belt
Maintenance
- Easy access to the rotor via the hydraulic opening in the casing
- Automatic greasing of rotor blades
- Essential maintenance is reduced to:
> Replacing the star cams
> Reloading the tips of the disks and anvils
> Replacing the shielding parts of the casing
> Cleaning the transmission - Quick mounting of wear parts
- Long working life and low maintenance costs
- GSM modem for remote diagnostics
Productivity
- Hopper opening for optimum feed by conveyor
- Rotor developed to favour material capture
- Several rotor configurations for different applications
- Adjustable grinding grading using different-sized star cams
- Efficient evacuation of shredded products by reinforced scrapers
Safety
- Compliant with the Machine Directive 2006/42/EC
- Feed hopper designed to avoid projections
- Fast evacuation of unshreddable material via exit door
- Protection of ventilation via overpressure vents
Available equipment
- Metallic feed conveyor slaved to the grinder load
- Acoustic enclosure
- Ventilation according to the products being processed
- Complete line with magnetic sorting
- Sorting booth

Applications