NF – Non-ferrous recycling plants
Used to process secondary aluminium material not suitable to be charged straight into the melting furnace, shredding brings material into size and density specification while the downstream equipment cleans the material, removing contaminants and fines material that would not be handled in the furnace. Danieli shredders can be installed in-line with decoating and melting furnaces to minimize material handling and reduce material stocking into the plant.
With Danieli Centro Recycling non-ferrous shredder plants, you can process all types of non-ferrous metals like aluminum, UBC, brass, copper, and more.
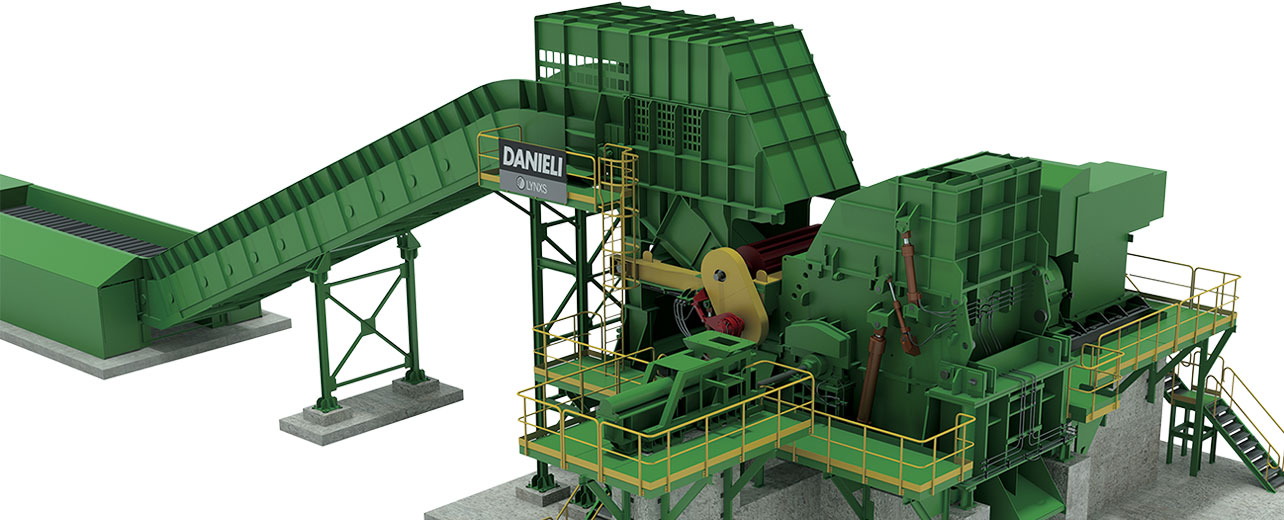
> High-inertia long-ife totally enclosed capped Rotor
> Heavy-duty Rotor Bearing Housings
> Rotor Lifting Device for easy and safe maintenance access
> High impact resistant Top Discharge Grid
> High impact resistant alloy steel liner plates
> Hydraulically opened & latched Top Section for easy and safe maintenance access to
> Clean low copper content high-density fragmentised steel scrap
> Open fragment form prevents non-ferrous inclusions
Effective separation and recovery
> Uniform fragment size allows non-ferrous metal separators to be set for narrow range and hence at their most efficient
> Automated recovery of high-value non-ferrous materials
> Lower transportation, secondary processing and handling costs
Efficient and cost-effective
> Uniform pulverisation allows unimpeded recovery of non-ferrous metals
> Enclosed conveyor system reduces and prevents wind spillage
> Copper wire fragments can be removed by metal sensing separator
Middle Section liner plates
> Hydraulically operated Top Discharge Grid Closing Door
> High-speed single-stroke hydraulic Hammerpin Puller
> Hydraulically fixed Anvil
> Single unified base structure for increased stiffness & strength in vicinity of anvil
> Inventive Lower Grid arrangement for increased discharge area
> Separate replaceable Chute Nose fabrication
> Separate replaceable Hinge Bracket between Base and Middle sections
> Modified Middle Section Side Liner wear plates for long life
> Reject Door
> New ring frame Compression Feeder configuration
> Integrated water based Dust Suppression System as standard
